国内製造業の「スマートファクトリー」事例
製造業DX ~モノづくりの常識を変える「スマートファクトリー」~<後半>
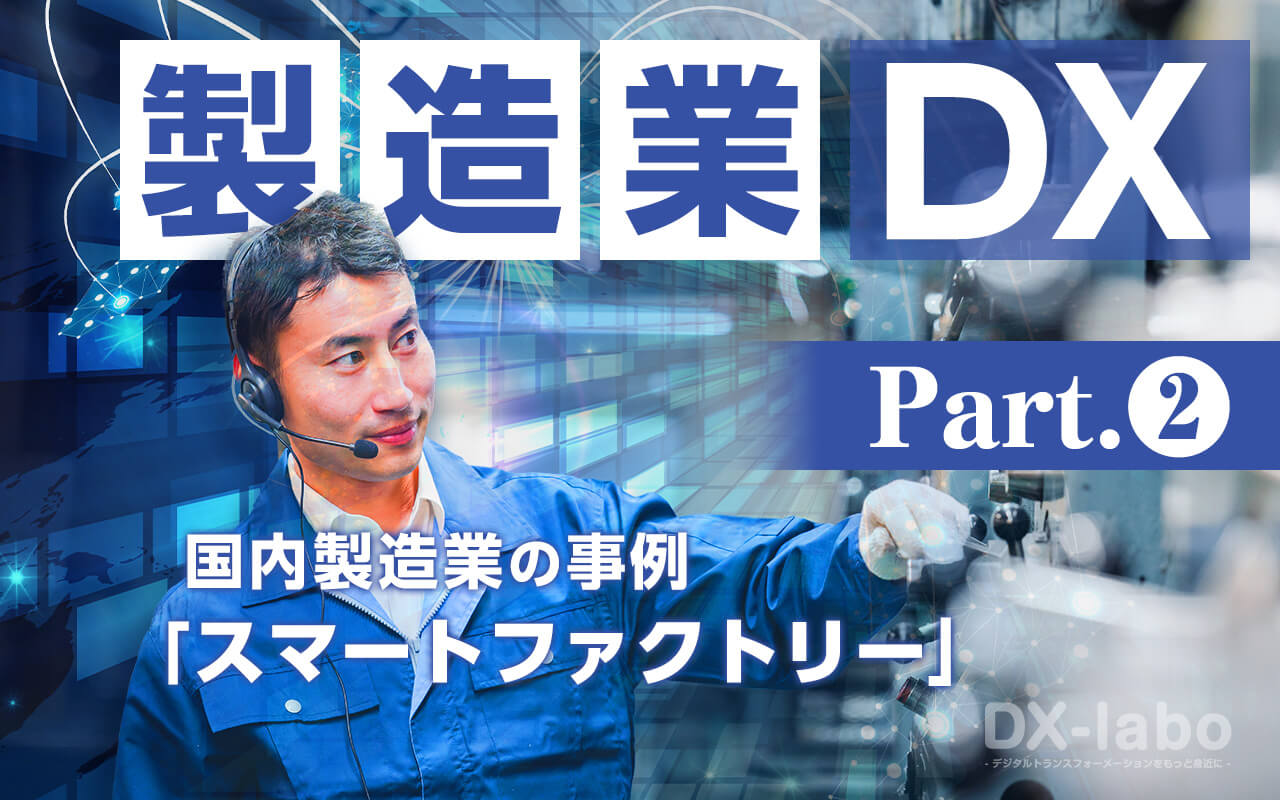
大企業も中小企業も
IT・デジタル技術を駆使したデータ活用によって、既存の“モノづくり”を変革するスマートファクトリー。日本での普及はまだまだこれからといった段階ですが、それでも少しずつ成果を上げている企業は登場しています。
日本初! 先進的なスマートファクトリー事例
日本の代表的なスマートファクトリーとして取り上げられることの多い工場が、株式会社日立製作所の大みか事業所です。早くも2015年に、IoTを活用したサプライチェーンと工場の生産活動のデジタル化を開始。現在では製品の開発・設計だけでなく、納入後の運用保守にまで至るバリューチェーン全体の最適化・高度化を実現しており、2020年1月には世界経済フォーラムより世界の先進工場の一つに日本で初めて認定されています。
同工場では、以前『デジタルツインとは?』という記事で紹介した、現実世界をデジタル空間上に再現するデジタルツイン技術も導入。無線通信を用いて様々な対象物を識別・管理する「RFID」システムなどを用いて製造ライン上の「人」と「モノ」に関するデータを自動収集し、デジタル上にそれらの流れを可視化することで、進捗把握や品質改善、設備不良の自動検出などにつなげています。
こうした取り組みにより、主力製品の生産リードタイムを50%短縮することに成功(設計工程で20%、調達で20%、製造で10%を削減)。同工場が目指しているのは、“需要の変化に即応して⼈員や部品などのリソ-スを最適配分しながら、⽣産全体の最適化と品質向上を図る⼯場”とのことですが、実現すればまさにダイナミック・ケイバビリティを具現化した工場と言えるでしょう。
参考:日本企業として初、日立の大みか事業所が世界経済フォーラム(WEF)より世界の先進工場「Lighthouse」に選出|株式会社日立製作所
参考:いま注目を集める「デジタルツイン」とは? 日立の活用事例も紹介|株式会社日立製作所
中小企業のスマートファクトリー事例
スマートファクトリーは決して大企業の専売特許ではありません。中には柔軟な発想と行動力で、大企業顔負けの大きな変革に成功している中小企業も存在します。その一つが愛知県の自動車部品メーカー、旭鉄工株式会社です。
以前は生産時間や設備の稼働状況などの生産管理に必要な情報を、すべて手作業でモニタリング(計測・記録)していたという同社。課題であった従業員への負担やヒューマンエラーを減らすためにIoTの導入を検討したところ、導入コストや自社設備の古さがネックとなり断念。そこで同種のシステムを自社でゼロから構築することにしたのです。
非IT企業ゆえ、社内に専門知識を持つ人材は皆無。それでも独学を重ね、遂にデータの収集と可視化を自動実行できるシステムを開発します。現場に導入したところ効果は抜群で、1時間当たりの生産個数が7割上昇。増設予定だった生産ラインが2本不要になり、1億4千万円分の設備投資費用が削減できたそうです。
その後は米大手ソフト開発会社の協力も得ながら1年ごとにシステムを刷新。さらに別会社を立ち上げ、中小製造業向けの外販や生産力向上のためのコンサルティングをスタートさせるなど、新規ビジネスの創出も実現しています。
スマートファクトリーによって広がるビジネスの可能性
スマートファクトリーによる業界共通課題の解決事例
IT・デジタル技術の活用により、製造業共通の課題である“技術継承”問題を解決した企業もあります。金型の製造・販売を手掛ける株式会社IBUKIは1933年創業と歴史ある企業。同社が工場デジタル化の軸とした技術がIoTとAIでした。
IoTを導入した業務の一つが金型成形作業。金型の内部に複数のIoTセンサーを埋め込み、成形中の金型内部の状況を数値化して把握できるようにしたのです。これにより、それまで同作業に携わっていたベテラン技術者のコツや暗黙知を“可視化”でき、技術継承が可能になりました。
AIでは、熟練者の思考をベースに構築したAIを搭載する「見積り支援システム」や、同じく熟練者の判断基準をベースにAIが工具の使用可否を判定する「工具摩耗判定システム」を開発。いずれのシステムも、自社で活用するだけでなく、中小企業などに向けて販売もおこなっています。
リーマンショック以降、一時は売上が激減したこともある同社ですが、これらの取り組みにより半年で黒字化を達成。その翌年には営業利益率10%まで回復したということです。
参考:DX取組事例 株式会社IBUKI|経済産業省 東北経済産業局
今回は触れられませんでしたが、スマートファクトリーでは他にも次のような技術が活用されています。
- ・作業を自動化・省人化する「産業用/協働ロボット」「AGV(自動搬送車)」
- ・熟練者の技術を追体験することで技術継承を実現する「VR(仮想現実)」
- ・作業者の視覚を管理者が共有することで遠隔作業を支援できる「スマートグラス」
- ・作業台などに作業指示を投射して作業を正しく誘導する「プロジェクションマッピング」
- ・大容量データの高速通信が可能でセキュリティも強固な「ローカル5G」
- ・センサーから取得したデータをクラウドなどの外部に送信せず、現場と近い末端(エッジ)で処理する「エッジコンピューティング」
上記以外でも、今後はサプライチェーン・マネジメントにおける運用コスト削減やデータ改ざん防止、トレーサビリティーの確保などを目的とした、「ブロックチェーン」の活用も増えてくるかもしれません。
また技術面以外では、事例の中でも出てきましたが、自社のスマート化で習得した技術・ノウハウを“サービス”として他社展開する企業のプレゼンスが高まっています。このように、“モノづくり”だけでなく、“コトづくり”や“プラットフォーマ―”のような新たなビジネスモデル創出の可能性を秘めているところも、スマートファクトリーの魅力の一つと言えるでしょう。
前半記事の冒頭で製造業を取り巻く外部環境と課題について触れましたが、それ以外にも、近年テック企業の参入が相次ぐ自動車業界のように、いつなんどき自社の事業領域にデジタルディスラプターが出現するかはわかりません。そういった意味でも、スマートファクトリーによるダイナミック・ケイバビリティの強化は、製造業であれば決して無視できるテーマではないはずです。